Active detection of asymmetry in turbo machinery via asynchronous excitation (Technion)
All heavy machinery relies on large shafts to convey rotary motion. A small shaft crack, if not detected in time, can cause instability which can render the machine unusable and in rare cases even explode. Current methods for locating faults in turbine shafts and generator rotors require either stopping the machine and exciting it with vibration, or passively monitoring system behavior while the machine is running. While the first method is fairly accurate, it requires shutting down the machine, resulting in large losses especially in critical applications like power plants. Passive monitoring is considered inaccurate because the vibrations caused by small cracks are usually not detected until it's too late.This invention combines the best of both methods mentioned above – by actively introducing tiny vibrations into the system while it is running and monitoring the system's response using a unique algorithm, it is possible to locate faults without causing system downtime. An external actuator applies vibration in a frequency relative to the rotation speed, causing foreign frequencies caused by deformations to be amplified by a factor of up to 100 and be detected in an external sensor even when the asymmetry is smaller than 1%.
• Total monitoring with zero down time
• No disassembly or direct contact with shaft required
• Reduces costly maintenance intervals of limited access areas like wind turbines and nuclear plants
• Continuous monitoring - instead of occasional periodic testing
• May induce smaller safety margin, which may increase safe operating range
Steam and gas turbines used in generating electricity, jet engine turbines, wind-turbine and other large generators, heavy pumping equipment in nuclear and other power plants, flywheel energy storage devices.
Israel
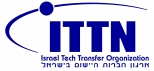